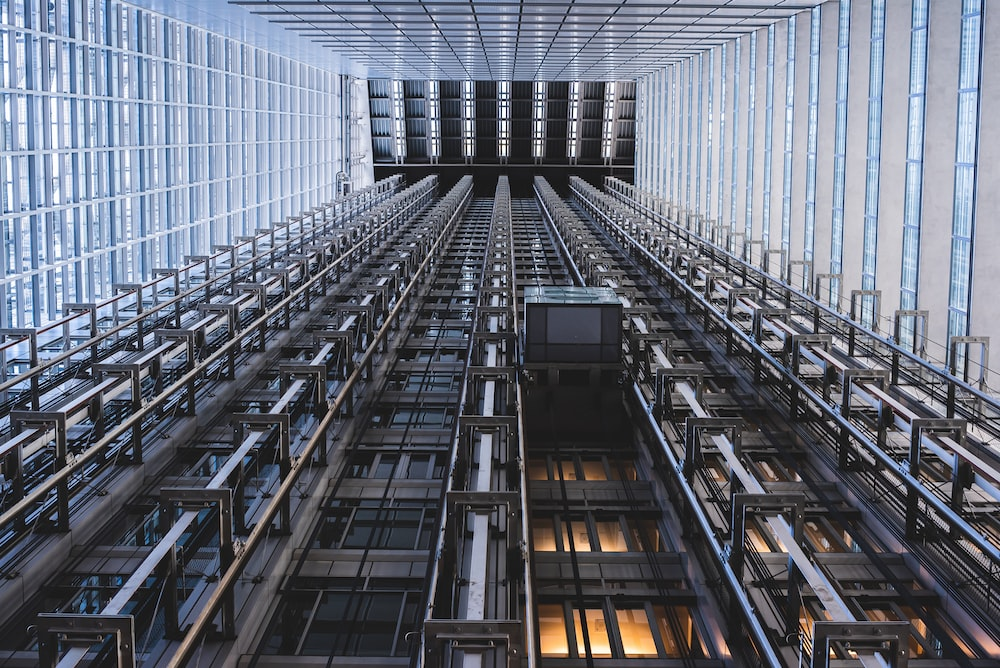
The buildings in New York City receive heavy footfall every day. Most people use elevators to move from one floor to another. This extensive usage of elevators leads to wear and tear that requires adequate maintenance to prevent any damage.
Every responsible building manager or owner understands the importance of preventative maintenance. A properly functioning elevator not only offers convenience and comfort to a building’s visitors but also keeps everyone safe.
As a leading elevator consulting firm in New York, our experts have shared some preventative maintenance guidelines for building owners.
What is Preventative Maintenance?
Preventative maintenance is a proactive approach that allows you to avoid potential issues and problems through adequate upkeep. This approach detects complications before they snowball into major problems, so you don’t have to bear costly repairs or any adverse consequences later. It includes regular elevator inspection with special attention to the motor, brake system, bearings and cables, pulley, brushes, drive sheaves, sensors, and roller wheels.
Elevator inspectors will look for signs of wear, existing faults, or potential defects. To address these issues, the technician will replace damaged parts, adjust existing parts, and thoroughly clean and lubricate the system.
Preventative Maintenance Guidelines for Busy Elevators
Daily Inspection
Besides professional comprehensive inspections, you need to perform daily inspections before starting the elevator. The designated elevator manager of the building should start the day by observing anything unusual in the elevator and getting necessary repairs. Here’s what you need to check:
- Are the buttons working properly?
- Is the elevator stopping on the right level with the floor?
- Are there any unusual noises as the elevator ascends or descends?
- Are the lights working fine?
- Is the control panel functional?
- Is the emergency phone working?
- Are the doors closing and opening correctly?
Adding these steps to your daily inspection schedule will not only ensure the elevator’s safe operation but also keep repair costs and calls down.
If you find any of these issues in the elevator, shut it down until it’s repaired. Inform people about the repair and non-operational hours of the elevator to minimize their inconveniences.
Inspect Elevator Doors
Doors are the most used and abused components of any elevator. Every day, passengers carry bulky baggage and carts, damaging the doors during loading and unloading. Sometimes passengers forcefully open the doors, affecting the sensors. The daily foot traffic accumulates grime and debris on the door sill. Debris (or any foreign object) can get stuck in the door track, affecting its function. Therefore, the elevator doors need extra attention.
Although modern elevator doors have a robust mechanical design, constant usage can cause many problems. Malfunctioning doors can fail to open, shut down completely, or go out of alignment. However, with periodic maintenance, you can identify signs of damage and get necessary repairs.
A simple step is to inspect the doors every day and look for scratches, unusual sounds, or improper functioning. Scratched elevator doors suggest that they are misaligned and causing panels to drag. A licensed elevator technician will readjust the doors and make necessary repairs. They will also clean the sill while ensuring not to disrupt the light curtain or other fragile components.
Lubrication
Insufficient lubrication in elevator rails can cause excessive vibration. This friction first creates unpleasant noise leading to downtime and other severe damage. Periodic sufficient lubrication eliminates friction between the rails when the elevator goes up and down. This helps you avoid maintenance costs and interruption and service.
Every elevator has different lubrication requirements specified in the manufacturer’s manual. Generally, you need to lubricate the motor, hoist ropes, ball bearings, machine roller, and gears. However, it’s crucial to use lubricants specified by the manufacturer. An elevator consulting service provider can help you determine the right time and product for lubrication.
Emergency Lighting and Communication
Emergencies can happen anytime, which is why you should always be prepared. Make sure your elevator has a battery backup system to continue operation during power failures. You should also incorporate emergency lighting and communication channels to keep your passengers safe during system breakdowns. Check these systems every now and then to ensure their working. If there are any issues, immediately call an elevator service provider for repairs.
Have a dedicated team who can respond during emergencies, such as power failure, system failure, misleveling, doors malfunctioning, etc. Getting stuck in an elevator can be difficult for many, so make sure you offer quick assistance.
Professional Cleaning
Besides regular cleaning, elevators require periodic deep cleaning from professionals. Research suggests that elevator buttons and handrails contain 40 times more bacteria than toilet seats.
Due to the closely packed space and hundreds of people using it every day, elevators carry a lot of germs and can easily infect a healthy person. While you may have a dedicated staff for elevator cleaning, it’s good to hire professional cleaners for thorough disinfection and cleaning. They will use special solutions and techniques to eliminate germs, bacteria, grime, or debris from each component of an elevator.
Professional Inspection and Testing
Professional inspections are different from regular inspections as they are more thorough. There are two major types of inspections, Category 1 and Category 5.
Category 1 Inspection
The NYC Department of Buildings (DOB) requires annual inspection of all elevators, known as the Category 1 (or CAT 1) test. Managers or owners need to hire a third-party elevator inspection firm for this test. It takes 2 hours and typically involves the inspection of:
- Safety devices
- Hoistway
- Communication devices
- Suspension cables
- Alarms
- Emergency Lighting
- Housekeeping of the elevator’s top, machine room, and pit
Category 5 Inspection
The Category 5 test is performed every five years and inspects all components as Category 1 test. But it also includes other elements such as:
- Electrical equipment
- Verification of full load
- Car safety devices
- Buffers operation
- Tripping speeds
- Ability to break and slip
Document Repairs and Inspections
Keeping a repair and inspection log can help simplify the maintenance process. Document each incidence of malfunction along with dates. In fact, the OSHA regulations for elevator maintenance also suggest posting the records of annual inspections near the elevator.
This data can assist building managers, cleaners, and technicians and help you determine required repairs.
Elevator Modernization
Modernization is more expensive than other repairs, and you can avoid it with adequate maintenance. However, sometimes there’s no other way to fix the elevator than to modernize it to prevent severe incidents. Elevators become worn out over time, and modernization helps eliminate all defects from the system.
For modernization, you need to make sure that the new elevator adheres to state and local regulations. This will give you peace of mind that your elevator will not break any time soon. Once you get the required replacements, make sure to follow all steps of preventative maintenance to keep the elevator in good shape for a long time.
HighRise Consulting offers a wide range of elevator services, including Category 1 and 5 testing, elevator inspections, and more. We are based in Brooklyn, NY, but also serve clients in various regions, including Staten Island, Manhattan, and the Bronx. Request an estimate or Contact us to book an appointment.
continue reading
Related Posts
Elevators are one of the most common ways to provide […]